The Littoral Combat Ships have been emblematic of the U.S. Navy’s struggles in integrating new technology into the American battle fleet.
AFP/GETTY IMAGES
The U.S. Navy is in a tough spot. Sailors need cutting-edge technology, but full-scale vessel, propulsion and large system-level prototypes needed to test new technological approaches are often considered too costly for Congress to fund. Instead, vessel innovation too often done on the fly, kludged onto new procurement projects after a bit of ad-hoc computer modeling, some brainstorming at the systems level, or via the savvy guidance of some influential salesperson.
Given that research and development hard to fund these days, Navy innovation aboard ships and subs are now frequently blended into big procurements as immature, untested and poorly thought-out subsystems. This corner-cutting habit of hiding research and development in a big, expensive vessel procurement or forcing new technologies into an ongoing combatant production run has a real cost. And today, after taking too many research and development shortcuts, the U.S. Navy is feeling the pinch as it shifts to confront a rapidly changing maritime threat environment.
With too few ships ready to deploy, any delay or misstep in technical design imposes immediate consequences on the U.S. fleet. And as rivals press ahead in building new and advanced combatants, U.S. Fleet Commanders need shipyards to produce battle-ready vessels at ever-faster rates. In this dynamic maritime environment, the last thing Navy leaders want is for new combatants to be sidelined over pesky technology problems or pulled off-track by inadequate systems engineering oversight. But, again and again, with the U.S. Navy’s two Littoral Combat Ship classes, the Zumwalt class destroyer, and the Ford class aircraft carrier, naval combatants are being delivered incomplete, unready for contested oceans.
Managing this tension between technological innovation and warfighting demands the institutional fortitude to make tough decisions and pay some substantial “up-front” developmental, test and prototyping costs. Even though the U.S. Navy needs platforms with the best possible technology, naval stakeholders cannot keep burying new combatants under a tsunami of new and untested high-tech gear, ceding the solid warfighting priorities of reliability, lethality, and simplicity to the whimsy of, say, a technology-intoxicated ex-Admiral.
The U.S. Navy must learn to say “enough”, and build combatants that work while directing new and untested ideas towards a vibrant, well-funded prototyping program.
New ideas are only great if they are proven out.
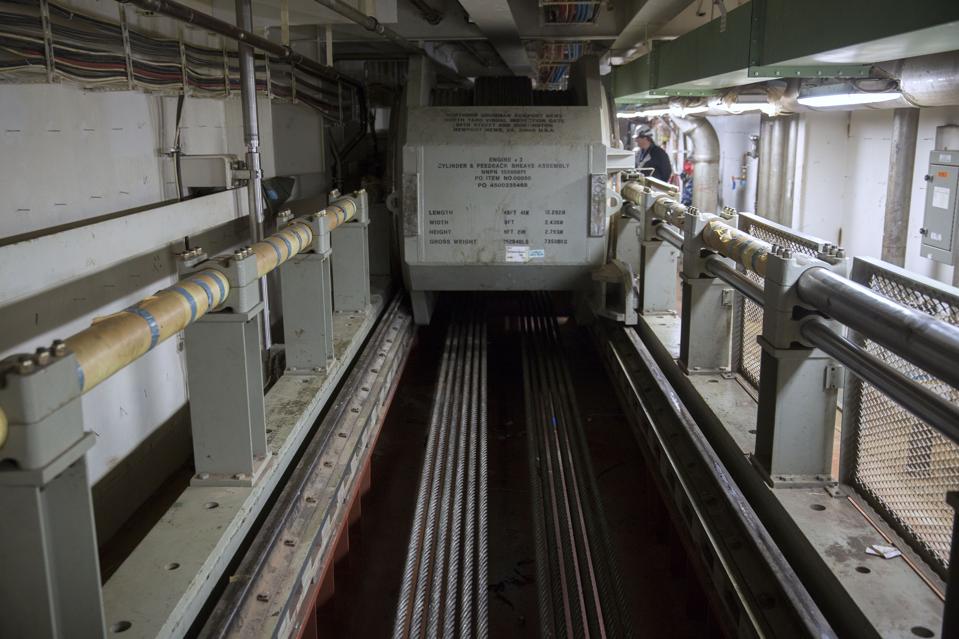
More than two years after commissioning into the battle fleet, the weapons elevators aboard the USS Gerald R. Ford (CVN 78) aircraft carrier have yet to work.
© 2014 BLOOMBERG FINANCE LP
There Is No Substitute For Rigorous Prototyping
America’s constant struggles with new naval ships demonstrates that the need for full-scale prototyping at the platform (ship and submarine) level and at the basic systems (engine, reactor, elevator, HVAC and so forth) levels have not gone away. Flashy cost-savings initiatives like computer models are wonderful tools, but they still struggle to capture integration risks and can be based on inaccurate or unrealistic performance data. Insight that a mundane welding technique is insufficient in a pipe bend, or that a platform cannot work in salt water, or that the system is simply not sailor-proof are often only discovered when the first examples are built and tested in realistic conditions.
These are problems that cannot be left to the first operating crew of a lead ship in a new class of combatants to discover.
Innovation is expensive. Prototypes are pricey things that take time to build and test, but iterating high-risk and untested technology into an active serial-production run or a big, important nuclear aircraft carrier or ballistic missile submarine is riskier and can be even more expensive. In fact, the Navy’s record of success in flowing new innovations into mainstream combatant production-lines is not particularly good. Contrary to what passes as conventional wisdom these days at the Naval Sea Systems Command, investments in prototypes or large-scale technological demonstrations make innovations easier and less costly, providing real-world feedback and performance data to inform computer programs that will, in time, anchor state-of-the-art model-based design.
It is a simple equation. Prototypes and tests drive down risk and cost while ensuring the warfighter gets workable, reliable weapons when and where they’re needed.
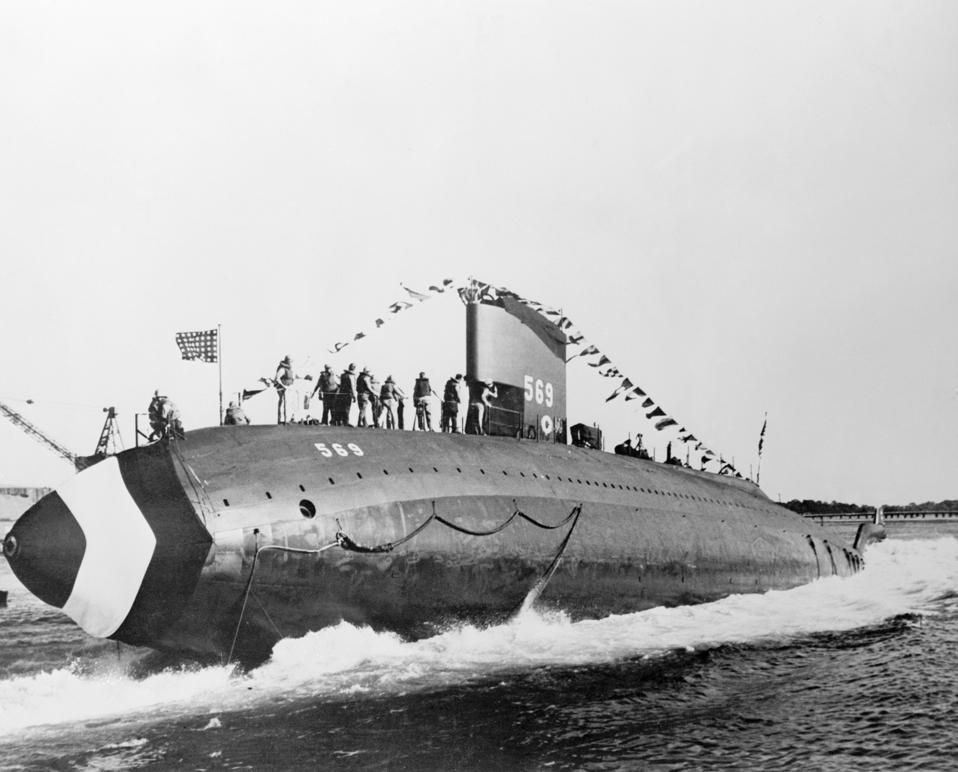
In 1953, the U.S. Navy launched the USS Albacore, an unarmed research submarine, testing a design that still informs modern submarine design.
BETTMANN ARCHIVE
Prototyping And Testing Drove Undersea Dominance
America’s undersea community has historically been far more comfortable in reducing shipbuilding risk by building and testing full-scale prototypes—or by dedicating valuable combatants to research and development duties as technology demonstrators. Investment in technology demonstrations have paid enormous dividends to the undersea community, helping the U.S. undersea fleet become an essential component of the American arsenal.
The Navy built and profited handsomely from systems-level and full-scale prototypes. The USS Albacore (AGSS-569), a full-sized unarmed research submarine, was built in the fifties to test and trial what was, back then, a cutting-edge teardrop hull-form. The lessons from the USS Albacore have informed U.S. submarines ever since. At a systems level, nuclear reactor designs of that era were traditionally tested ashore to gather data and assess the validity of the models and engineering analyses used in the reactor design.
The Navy’s investment in undersea technology demonstrators has been immense. About ten percent of the 225 nuclear attack and missile submarines America has built or put on order were, in essence, full-scale test articles, reducing overall procurement and operational risk. America’s first two nuclear submarines, the renowned USS Nautilus (SSN 571) and the relatively unsuccessful USS Seawolf (SSN 575), were more prototypes than battle-ready units. The innovative USS Tullibee (SSN 597) tested design suggestions from a high-level National Academy of Sciences research team. It is hard to imagine that similar high-risk maritime projects would be funded today.
But the submarine community’s constant drumbeat of technology “demonstrations” and rigorous testing have paid enormous dividends to both America’s industrial base and to the Department of Defense. Before the U.S. Navy started plowing taxpayer money into the successful sixty-two-hull production run of the Los Angeles class submarine, Congress allowed the undersea community to field the experimental but battle-ready USS Narwhal (SSN 671) and the USS Glenard P. Lipscomb (SSN 685) to test—and ultimately reject—new propulsion ideas. Other active-duty submarines were regularly pulled out of service and modified to test various smaller subsystems.
Today, the submarine community’s proud and proven testing legacy is in peril, out of favor in both Congress and the wider naval community. Rigorous technology demonstrations at the system or platform levels have been de-emphasized in favor of burdening new maritime platforms with an enormous amount of “on-the-fly” technological development, forcing the incorporation of risky new technology during the building process. But, with the enormous problems the $13 billion dollar super-carrier USS Gerald R. Ford (CVN 78) has had in integrating new technologies, Congress and the U.S. Navy are, hopefully, learning that the complexity and scope of some technological innovations are simply too vast to be introduced to critical, combat-bound ships on the production line.
This is not to say every new technology needs to be built ashore before it can be incorporated into an operational platform. The advent of model-based design, which is being used widely in commercial industry, can enable the development and integration of new technologies without having to construct a full-scale prototype. The accuracy of these models, however, depends on real-world data for system performance that naval stakeholders often do not have. Prototypes and tests can provide that data to enable improved modeling that could, in time, reduce the need for full-scale demonstrators of future systems.
Making matters worse, the Navy has made it very hard—if not impossible—for anyone to reliably enumerate the cost imposed by “innovation” during production. Innovation “on the fly” has attendant costs and technical difficulties. The Navy must do more to be clear about these developmental costs so analysts can conduct effective comparisons with old-school, “fly-before-buy” prototyping or technology demonstrations. Full-scale technology demonstrations are costly and slow, but they do work—and if the Navy didn’t take such pains to hide their financial data, even the least-talented Congressional analyst could offer a compelling fiscal case for a more prototype-heavy and research-and-development oriented investments in shipbuilding.
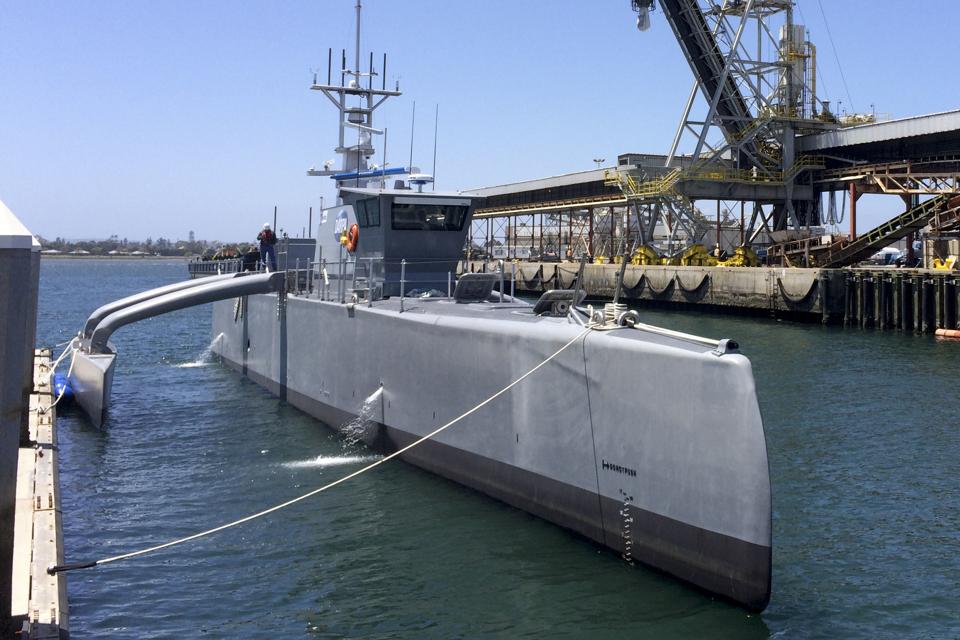
The Pentagon is testing the Sea Hunter, an unmanned surface vessel.
ASSOCIATED PRESS
Keep Building Autonomous Prototypes:
All is not lost. Prototyping is far easier in the unmanned space; the technology is so new, prototypes offer the only path forward. The relatively small size and relative cost of modern unmanned craft also makes the investment far less odious. Essentially, it is easier and and less costly to design, build, test, trial and then discard a small platform.
The Navy’s recent program to develop an unmanned combat air system demonstrator (UCAS-D), the X-47B, is an informative example. “The Navy fielded two X-47Bs in 2012 to validate the design of its autonomous controls and systems designed to land the UCAS-D on a carrier at sea,” said Bryan Clark, a well-regarded Senior Fellow at the Center for Strategic and Budgetary Assessments. “The X-47B also demonstrated the ability of an autonomous aircraft to navigate the flight deck under the direction of crew members. Although the Navy incorporated lessons from the UCAS-D into the control system for its new MQ-25 Stingray unmanned refueling aircraft, it did not choose to transition the UCAS into production. This decision may have reflected a reticence to incorporate an unmanned combat aircraft into the carrier air wing.” In other words, the Navy learned from the prototype and then put it aside.
The Navy is also racing ahead with autonomous surface vessels. The Defense Advanced Research Projects Agency (DARPA)-funded Sea Hunter is set to be followed by an array of unmanned surface vessels of various sizes. But rather than being content to to fully tap the diverse and thriving industrial base to continue building and testing prototypes, the Navy is facing pressure to limit competition by scaling up and feeding a few builders contracts for “block buys” of several identical experimental vessels. The Navy should recognize that autonomous technology and tactics needs more time to mature, and the field may benefit far more by enabling several different approaches to autonomous sailing to develop rather than, at this early stage, flooding a single approach with all the available funding.
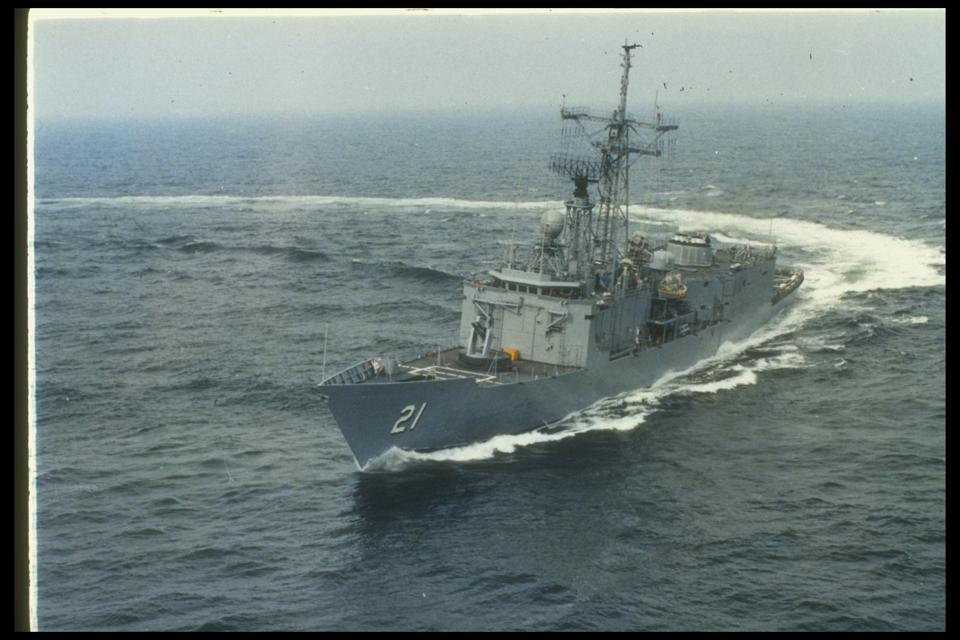
Successful Cold War Combatants like this Oliver Hazard Perry Class frigate benefitted enormously from full-scale prototyping and real-world tests of various systems.
THE LIFE PICTURE COLLECTION VIA GETTY IMAGES
Conclusion: Make The Up-Front Investment
Rather than descend down an operational spiral, where ships and submarines are in such demand that they cannot support prototyping and technology development at the system level, naval stakeholders must recalibrate their platform demands to ensure sufficient hulls and on-shore testing facilities are available to test and trial new systems—if America wants to really drive innovation in battle fleet platforms, then the Navy needs the hulls and the funding to do it correctly.
It is expensive work, but it can be done. Two combatants (USS Talbot (FFG 4) and USS Dale (CG 19) were used to test and trial components that, ultimately, came together in the successful Oliver Hazard Perry class frigate. Testing was extensive; The new frigate’s prototype propulsion system was built on land and taken for artificial cruises, and the new combat system was tested out on land with only the frigate’s gun, missile launcher and sonar simulated. According to a March 1978 U.S. Naval Institute Proceedings article by Captain John Beecher, an Oliver Hazard Perry class Program Manager, “the operational evaluation on land revealed some significant deficiencies” that forced a rebuild of the combat system. Even then, the new frigate needed some tweaks and changes before evolving into well-liked and reliable sea fighters. Testing new technologies and trialing new prototypes at the system and platform level before a new ship is built offers a worthy return on investment.
Certainly, full-scale prototypes are up-front costs and complex management challenges that lack Congressional support, but more stakeholders must understand that savvy prototyping and testing can help keep the industrial base humming and the voters happy. Ultimately, vigorous tests and trials that come from technological demonstrations will save the U.S. Navy an enormous amount of money, ships and sailors. It’s time to do more prototyping.
[“source=forbes”]